EPITAN 92
Epoxy tank coating
- Chemical resistant
- Corrosion protective
- Immersion resistant
- Low-temperature curing
- Water resistant
- 2-component
- Solvent-borne
- DTM (direct-to-metal)
- Primer
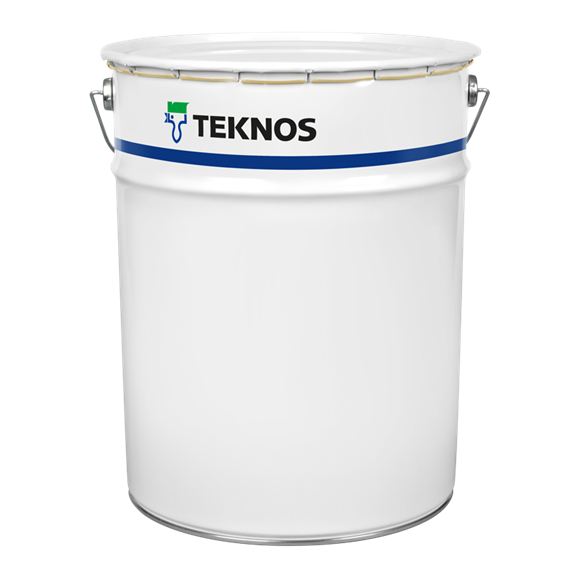
- Chemical resistant
- Corrosion protective
- Immersion resistant
- Low-temperature curing
- Water resistant
- 2-component
- Solvent-borne
- DTM (direct-to-metal)
- Primer
Modified epoxy primer, flake materials pigmented, thixotropic, high solid, two component, cured in low temperatures (from -10°C).
For priming of steel constructions operating in sea, coastal, technical and fresh water, underwater parts of ships, docks and hydrotechnical constructions. For self-protection of ballast and sewage tanks, steel constructions operating in water or in ground (canal locks, culverts, weirs, dolphins, tanks, pipelines, quays, Larsen walls, etc.) Coating with outstanding adhesion to surfaces, resistant to acid and alkali solutions, water and marine environment, aggressive atmospheric conditions, soil and elements occurring in the cathodic protection.
Technical data sheet
Surface preparation
Before cleaning of surface, it is recommended to wash it with water with addition of OLICLEAN 123 and then rinse with fresh water. The surfaces are prepared according to the different materials as follows:
STEEL SURFACES: The surface to be treated must be dry, salt-, grease- and dust-free, cleaned to the degree of cleanliness according to ISO 8501-1: Sa 2½ for submerged areas or at least St 3 for external surfaces. For internal surfaces at least Sa 2½. Porous surfaces should be primed with thinned EPITAN 92 paint. Coating gets the highest mechanical and chemical resistance by applying directly to sandblast cleaned steel surfaces (cleanliness at least Sa 2½).
COATING OF EPOXY PAINT: The surface to be treated must be without any rust, dry, salt-, grease- and dust-free.
Additional instructive information for surface preparation can be found in standards EN ISO 12944-4 and ISO 8501-2.
Application
Take into consideration the pot life of the mixture when estimating the amount to be mixed at a time. Before application the base and hardener are mixed in right proportion. Stir thoroughly down to the bottom of the vessel. Mixing by machine is recommended, for example a slow-rotating hand-drill equipped with a mixer. Inadequate stirring or incorrect mixing ratio results in imperfect curing and impaired film properties.
Apply by airless spray or brush. When using a brush it may be necessary to apply several layers to achieve recommended coating thickness.
Airless spray parameter:
Nozzle size 0.019 – 0.025"
Nozzle pressure 20 - 25 MPa
When preparing painting specification, depending on subject and type of construction, different dry film thickness than recommended can be assumed. During airless spray application typical dry film thickness range is between 150 and 250 µm. Different dry film thickness than recommended causes change in theoretical spreading rate, wet film thickness, weight of dry film thickness, drying time, overcoating time and ready for handling time.
In high corrosive environment it is recommended to prepare surface as best as possible and to apply successive layers of paint before full curing of previous layers to achieve best protection.
Application conditions
During the application and drying period the temperature of the ambient air shall be above -10°C, of the paint should be over +15°C and the relative air humidity below 95%. The minimum temperature of the surface shall be above -5°C (frost- and ice-free surface) and at least 3°C higher than dew point of the ambient air. Adequate ventilation during application and drying period is recommended.
Storage
The storage stability is shown on the label. Store in a cool place and in tightly closed containers.
Total mass of solids | abt. 1300 g/l |
---|---|
Volatile organic compound (VOC) | abt. 300 g/l |
Pot life | 3,5 h (+23 °C) |
Mixing ratio | 100:18 by volume (comp. A : comp. B) |
Hardener | Comp. B: UTWARDZACZ 076/077/087/EPITAN 92 |
Gloss | Semi-matt |
Practical spreading rate | The values depend on the application technique, surface conditions, overspray, etc. |
Drying time – dust free | after 2 h |
Drying time – touch dry | after 5 h |
Drying time – fully cured | after 2 days |
Thinner | TEKNOSOLV 9506 |
Clean up | TEKNOSOLV 9506 |
Colours | TO-990 black |
Safety markings | See safety data sheet. |