INERTA 266 (EPITAN 66)
Antistatic epoxy tank coating
- Chemical resistant
- Conductive (ESD)
- Corrosion protective
- 2-component
- Solvent-borne
- DTM (direct-to-metal)
- Primer
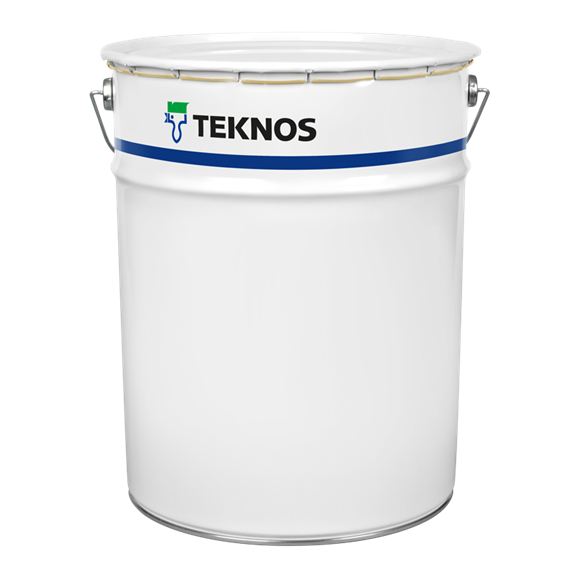
- Chemical resistant
- Conductive (ESD)
- Corrosion protective
- 2-component
- Solvent-borne
- DTM (direct-to-metal)
- Primer
High solid epoxy paint, thixotropic, two component, cured with amines, containing conductive pigments.
For the protection of inside linings of tanks, cisterns and pipelines for flammable liquids, also in explosion hazard zones. For protection of inside linings of tanks, cisterns and pipelines for liquid and loose products forming explosive mixtures. For protection of laminate constructions and other non-conducting surfaces for its antielectrostatic finish. Coating with outstanding adhesion to steel, laminates and mineral surfaces. Coating resistant to mechanical factors, oil, fuel oil, heating oil, diesel, motor gasoline, ethyl gasoline, unleaded petrol, biofuel, aviation fuel, glycol, glycerine, aromatics, water, electrolyte solutions and weathering. Coating is anti-electrostatic conductive material and with the provision of proper grounding is incapable of reaching a state of electrification. The surface resistance Rs of the coating is about 10exp.6 Ω, the leakage resistance Ru is about 10exp.4 Ω, measured according to EN 61340-2-3:2016-11. The coating of the paint, as well as the laminate based on it, meets the requirements of protection against static electricity related to hazardous areas. The coating meets the requirements of the standard TRbF 401.
Surface preparation
Application
Application conditions
Storage
Volatile organic compound (VOC) | Approx. 210 g/l using INERTA HARDENER 7272 (DIRECTIVE 2010/75/EU) The VOC value provided is the average value for factory produced products, and consequently it will be subject to variations between individual products covered by this Technical Data Sheet. |
---|---|
Pot life | 1 h (+23 °C) |
Mixing ratio | 10:3 by volume (comp. A : comp. B) |
Hardener | Comp. B: INERTA HARDENER 7272 |
Gloss | Semi-matt |
Practical spreading rate | The values depend on the application technique, surface conditions, overspray, etc. |
Drying time – dust free | after 6 h |
Drying time – touch dry | after 8 h |
Drying time – fully cured | after 7 days |
Thinner | Undiluted. Not needed. In exceptional circumstances use TEKNOSOLV 9506. |
Clean up | TEKNOSOLV 9506 |
Colours | TO-290 brown, TO-930 dark grey NOTE! Sunlight and chemicals cause the colour and glossiness to change in time. |
Safety markings | See safety data sheet. |