INFRALIT EP 8027-00
Epoxy powder
- Powder coating
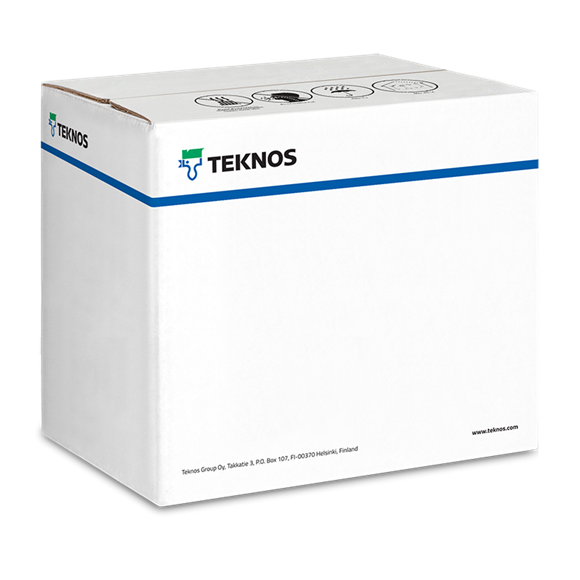
- Powder coating
INFRALIT EP 8027-00 is a powder coating based on epoxy resin, which at elevated temperatures melts, cures and forms the final paint film.
Used for product coating within the metal industry, e.g. for lighting fixtures, apparatuses, furniture, shop outfittings, agricultural and household appliances. Also suitable for use on many special areas in the heavy metal and chemical industry. The resultant paint film has excellent mechanical properties, i.e. good abrasion and impact resistance and elasticity. It is not scratched easily and withstands action by acids, alkalis, greases and solvents. Its anticorrosive properties are also good. On outdoor exposure the paint film has a tendency towards chalking. This phenomenon, however, affects only the appearance, not the protective power. An alternative material for outdoor use is INFRALIT Polyester Powder, which chalks only very little.
Surface preparation
Application
Storage
Practical spreading rate | 4 - 15 m²/kg depending on the film thickness |
---|---|
Spraying | TRIBO/CORONA |
Curing time | 10 min/200°C (metal temperature) |
Colours | By agreement. |
Packages | 15 kg or 20 kg according to the density of the powder. |
Safety markings | See safety data sheet. In order to avoid the discharge of powder from the booth into adjacent working spaces, the speed of air flow in the apertures of the booth must not fall below 0.5 m/s. Spray painters should wear dust masks and protective gloves. Any spatter of powder on the skin should be washed off with water and soap. |
Gloss value | 20-30 |